Rapid Manufacturing on Demand
1 to 1000+ Metal and Plastic Parts
Global delivery as fast as 10 days
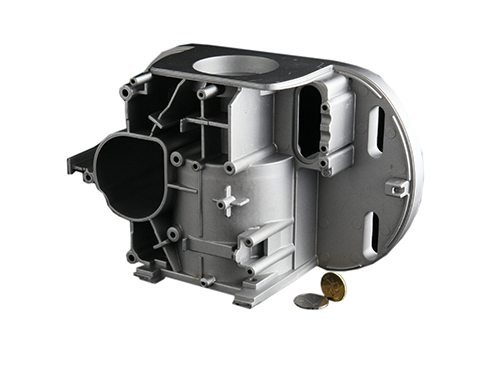
In a process similar to injection molding, we use certified machines and pressure casting dies to form molten metal into your designs. Our pressure die casting process is effective and very reliable. This method can actually end up saving you money. The majority of our castings are made from zinc, copper, aluminum, magnesium, lead, pewter, or other tin-based alloys. Because of our flexibility, we can accommodate any need you may have – from small batches of 50 to as many as 1,000 pieces.
Benefits
- Since die casting mold tooling can be more expensive and difficult to make, this method is suited for larger production runs, keeping the price for parts produced lower.
- Surface finish and dimensional stability are excellent.
- Complex geometries can be made that require little or no post-machining.
- It is great for medium- to larger-sized parts that would be slower and more expensive to machine.
Material
- Aluminum Die Casting
- Used to produce light but strong parts.
- Zinc Die Casting
- Zinc is used to produce ductile plated parts.
- Magnesium Die Casting
- Recommended for producing light parts that require excellent strength but must keep the weight in check.
Surface finishing
We have a variety of surface finishing options available; the choice depends solely on the type of component being produced and consumer preferences. Available options include: Sandblasting, Polishing, Plating, Painting, Powder coating, Pad printing, and Silk-screening.
3ERP advantages
3ERP offers a high-pressure die casting service to process high volumes of metal components at better tolerances and with excellent smooth finishes. If you need components that cannot be produced by other methods like vacuum casting and CNC, call our customer service now and get a quick, accurate quotation for pressure die casting.